Exothemic Welding
Introduction
The exothermic welding process is a simple, self-contained method of forming high quality electrical connections. The compact process requires no external power or heat source, making it completely portable. An exothermic connection is a molecular bond formed between two metals such as copper to copper, copper to steel and steel to steel. Connections are made inside a semi-permanent graphite mold, using the high temperature reaction of powdered copper oxide and aluminum.
The result is an exothermic reaction that produces molten, super-heated copper and aluminium oxide slag. The molten, super-heated copper melts the objects being connected, forming the molecular bond. The connections current carrying capacity is equal to or greater than that of the conductors being joined as there is no increase in resistance, unlike in most pressure type (bolt/crimp) connections. Because the connection is a fusion of high conductivity, high copper content alloy, it will withstand repeated fault currents.
Benefits of Exothermic Welding
- The weld does not deteriorate with age and time.
- Ability to withstand repeated high fault and surge currents
- Lower electrical resistance compared to a mechanical joint
- The connection will not corrode or loosen as it is a permanent molecular bond
- Widely used on copper to copper, copper to steel, steel to steel connections
- Also used on galvanized steel, stainless steel and copper clad steel connections.
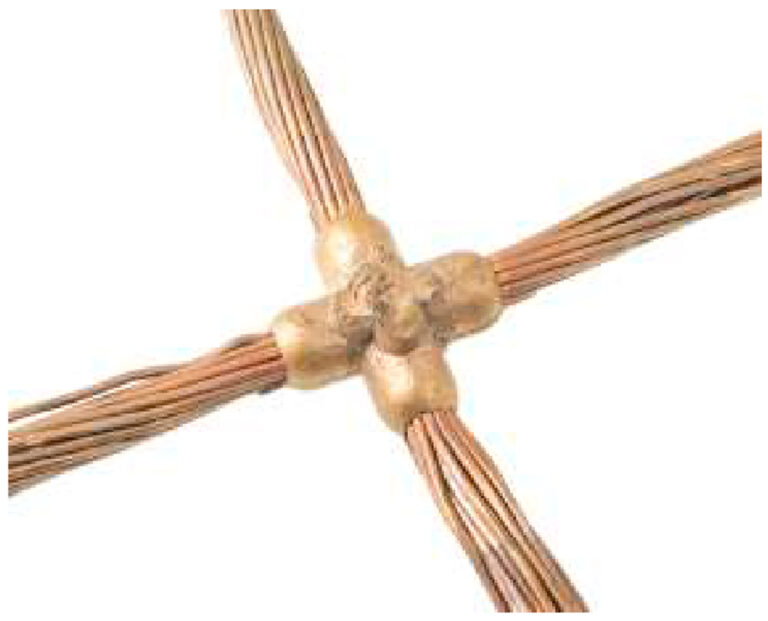
Mould
A graphite mold Is used for exothermic welding connections. The molds manufactured from graphite are strong enough to withstand the very high thermal and mechanical shocks present in the exothermic welding process. The heat obtained in the weld process is in excess of 2000°C. Graphite lends itself into easy machining to accommodate the various sizes and shapes required for welded connections. The mold life will vary according to the care given to the mold during use, cleaning, storage, and transportation.
- No alterations to be made to the mold
- Always clean the mould after every weld
- The graphite mold is designed to last for an average of 50 connections
- Keep the mould dry and away from any moisture
- Always refer to the mold name plate.
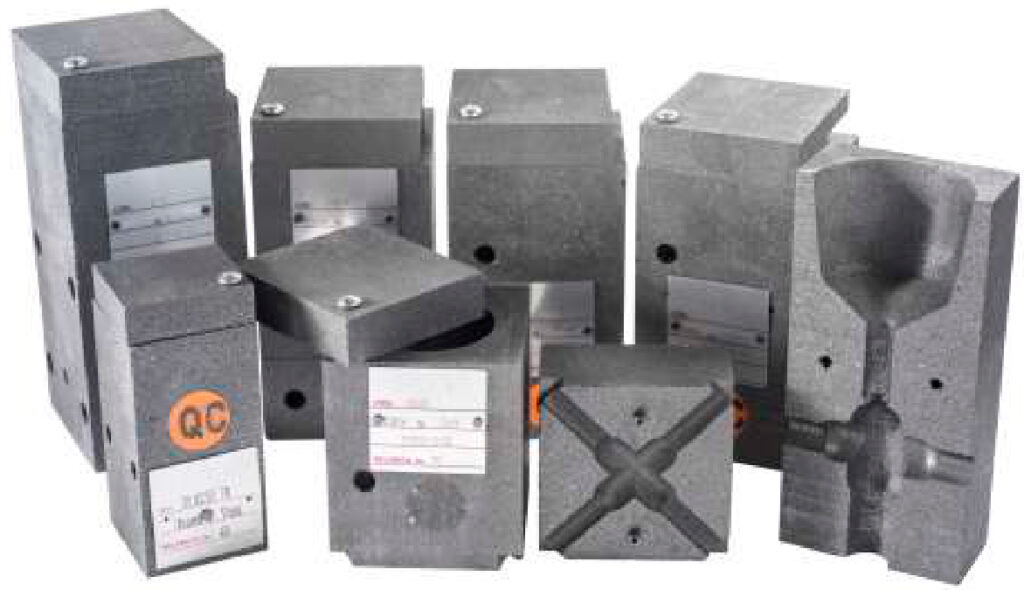
Weld Metal (Powders)
Weld metals consist of copper oxide, aluminium and flux in powder form. The powders are packed into plastic containers and the quantity is pre-determined for specific connections. The weld metal powders are marked in numbers, e.g. 15, 25, 32, 45, 65, 75, 90, 115, 150, 200 and 250g. These are packed with a lid, metal discs and silica gel which serves as a moisture absorber. The weld metal is packed under the white cap followed with the ignition power under the red cap. The ignition temperature of the weld metal powder is in the vicinity of 1000°C. This high ignition temperature is difficult to achieve, hence we use ignition powder. This ignition powder is similar to the weld metal, with the exception that it is much finer, allowing ignition at about 450°C by using a flint gun (igniter). Ignition from matches, cigarette lighters etc. is strictly prohibited. Each size of weldmetal container is application specific.
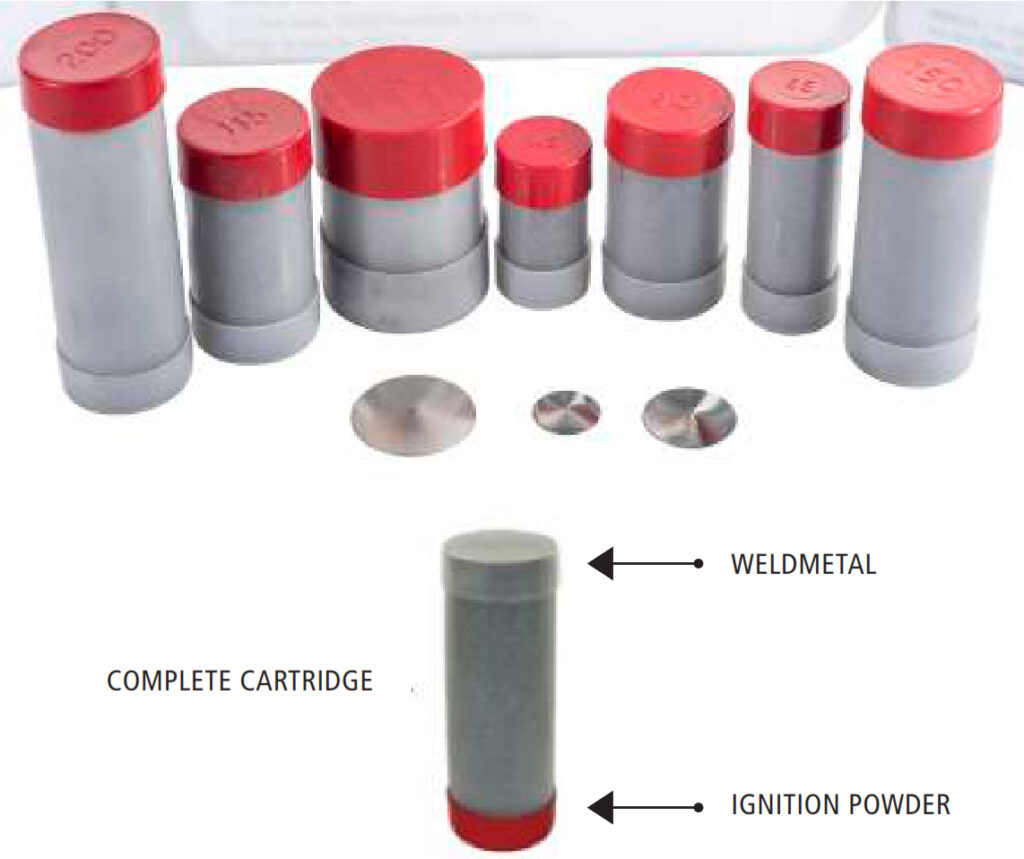
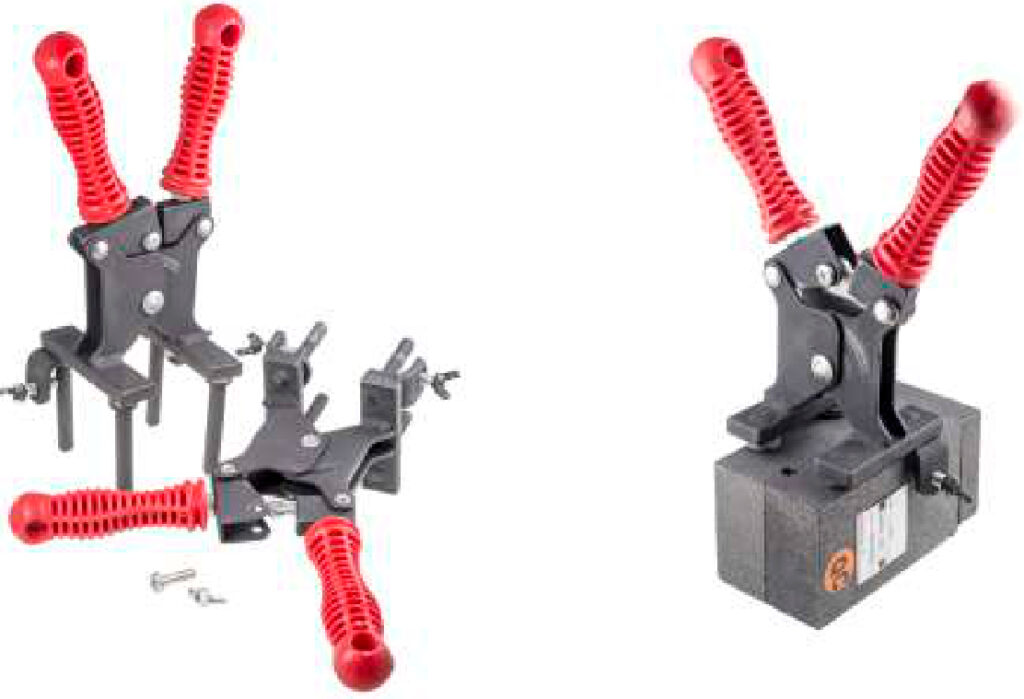
Handle Clamps
Handle clamps are essential part of the welding process for the following reasons.
- Handle clamps are equipped with vice grip locking arrangements which allows the operator to handle the mold efficiently.
- Repetitive welding process adversely raises the mold temperature making it difficult to handle the same effectively. Wear safety gloves and always use a handle clamp.
Tool Kit
The Tool Kit contains the necessary tools and accessories for carrying out repeated no of respective exothermic welding connections. The general tool kit contains the following parts:
- Plastic tool box
- Mold scraper 34
- Mold scraper 55
- Mold scraper 65
- Mold cleaning brush
- Conductor cleaning brush
- Toolkit Flint ignitor gun
- Sealing putty 160mm long 500g
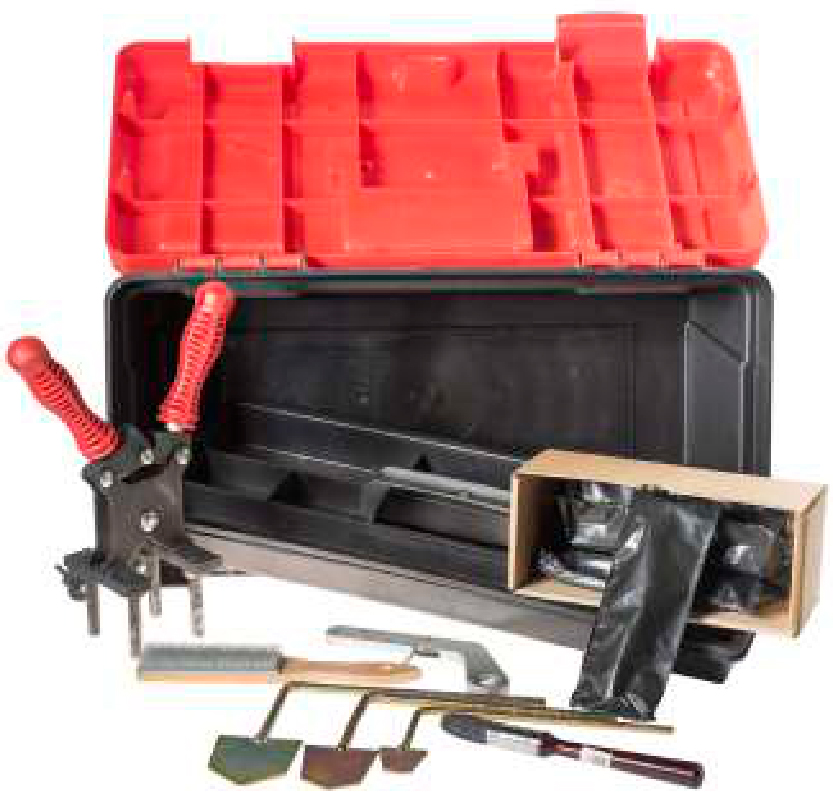
Welding Process
Step 1
Graphite is brittle and can break when dropped or hit. Please handle with care. Clean conductors using a conductor cleaning brush with a wooden handle and steel bristles provided.
Step 2
Select the correct mold by checking all the details on the mold name plate.
- Connection type
- Conductor Sizes
- Weld metal Size.
Step 3 (Fig. 1 and 2)
- Fit the conductors into the mould
- Close the moould with the handle clamp and lock
- Ensure the two mould faces seal (with no gap)
- Ensure that the conductors have a 3mm gap between them
Step 4 (Fig. 3 and 4)
- Slide the mould lid open
- Place the disc into the mould cup making sure that it sits properly
- he disc plays a very important role in sealing the tap hole, preventing any weld metal passing into the weld chamber. Should weld metal run past the disc, further procedures must be discontinued, as it will result in an unsatisfactory connection
Step 5 (Fig. 5 and 6)
- Remove the grey cap from the weld metal container, holding it over the cup of the mould.
- Slowly pour the weld metal powder into the cup, making sure not to upset the disc.
- The entire contents of the container will be filled into the cup. If incorrect amount is used, it will produce undesirable results.
Step 6 (Fig. 7 and 8)
- Check where the opening on the mould cover is located when in a closed position.
- Remove the red cap from the bottom of the weld metal container and sprinkle the starting powder over the weld metal and on the lip of the mold.
- Slowly slide the cover into the closed position, make sure not to wipe off any of the ignition powder.
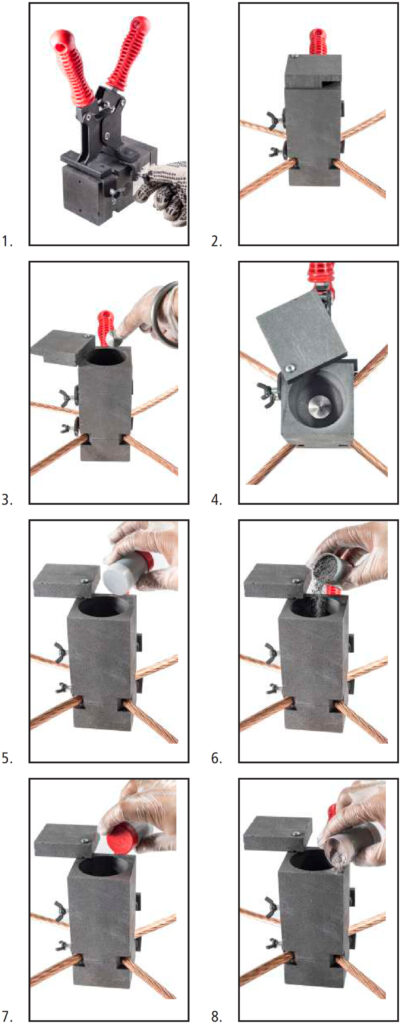
Welding Process
Step 7
Ensure the following prior to ignition:
- Wear all safety gear (gloves, goggles, etc.)
- Be well clear of all flammable goods
- Operators should be placed behind the opening of the mould cover
- Rest the flint igniter at approximately 60° on the lip of the mould where the ignition powder was deposited
- Ignite using the flint ignitor (Fig. 11)
Step 8 (Fig. 12 and 13)
- After ignition, wait 15 seconds before opening the mould with the handle clamp
- Remove the mould and handle clamp from the connection
- The smoke coming from an exothermic weld has been tested and found to be non-toxic
Step 9 (Fig. 14)
- Once the mold has been removed from the conductor, clean the mould using the mould cleaning brush
- This brush is used on all moulds (vertical and horizontal)
- Remove all remaining slag
Step 10 (Fig. 14)
- Use the mould scraper to clean up, this ensures minimum damage to the disc seat.
- The scraper is used for cleaning the cup and tap hole only on the horizontal opening mould
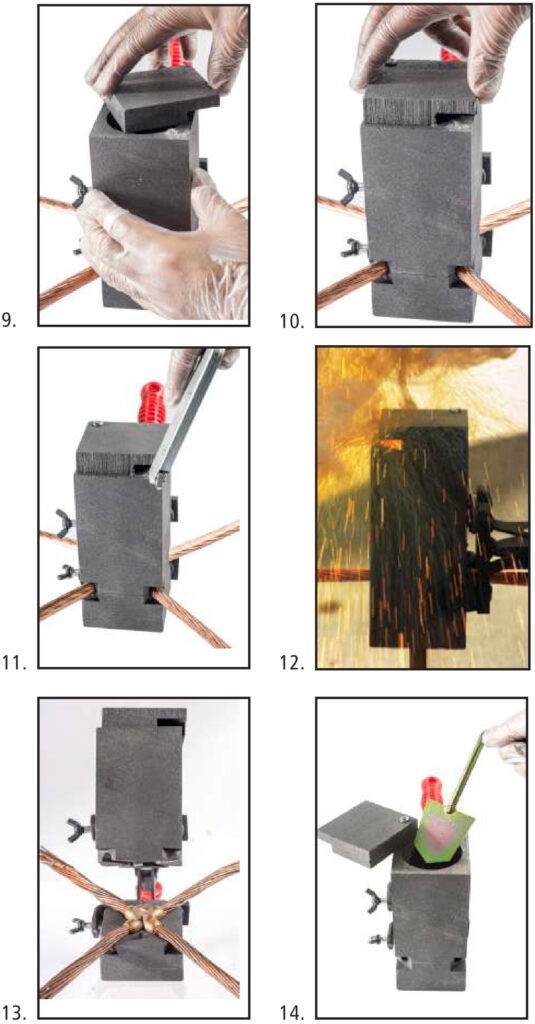